Low Flashpoint Solvent Machine
For precision component cleaning applications particularly validated processes.
Demonstration of IPA (Isopropyl alcohol) Cleaning and Drying System
The Layton Low Flashpoint (Flammable) Solvent and Vapor Degreasing system works with a two-tank design—Boil Tank and Process Tank—to provide efficient cleaning through a thermally controlled vapor process.
The Boil Tank may be sized to allow for the immersion of parts or may be smaller and off-set to minimise the quantity of solvent required.
The choice of configuration is, generally, dependent upon the level of contamination to be
removed from the parts.
Here's a breakdown of how the system operates:
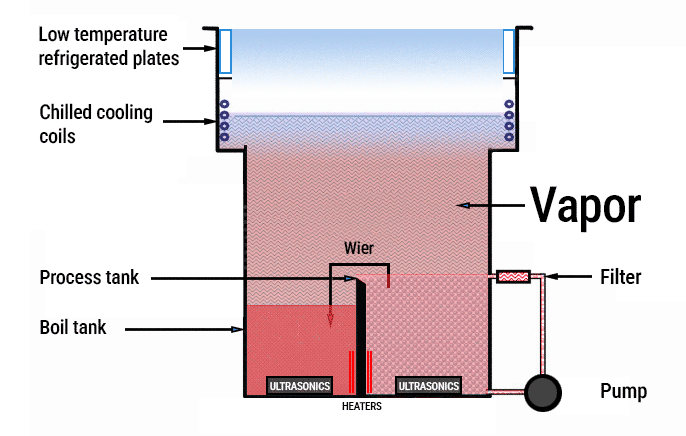
Vapor degreaser diagram image copyright Layton Technologies
System Components & Their Functionality
1. Boil Tank:
- The Boil Tank is responsible for heating the solvent to its boiling point to create the vapor. This tank is located off-set and does not allow for immersion of parts, which keeps the process gentle and controlled.
- The solvent is boiled to produce a vapor blanket that fills the vapor zone. The condensing coils in this vapor zone collect the vapor, causing it to condense and drip back into the Process Tank.
2. Process Tank:
- The Process Tank holds the solvent, which is constantly replenished by the condensed solvent from the vapor zone. The tank is designed with a weir, which allows the solvent to overflow into the Boil Tank, completing the solvent cycle and ensuring constant distillation of the cleaning fluid.
3. Work Carrier & Loading:
- Components to be cleaned are placed in a work carrier (often a perforated tray or basket), which is then positioned onto a work carrier nest at the load position.
- The process starts when the operator presses the cycle start button. This triggers the carrier to move down into the freeboard zone, which is just above the vapor zone.
4. Sealed Sliding Lid:
- Once the carrier is in position, the system seals the lid, creating a closed environment to ensure proper vapor containment. The lid remains sealed throughout the cleaning process to maintain the vapor pressure and to ensure the effectiveness of the cleaning.
5. Immersion & Vapor Zones:
- After the lid is sealed, the carrier automatically descends into the immersion zone of the Boil Tank, if the system is designed with a boil tank sized to accept parts or into the Process Tank. In this zone, the parts are exposed to the solvent, allowing it to remove grease, oils, and other contaminants.
- If equipped with ultrasonic agitation, it may be activated at this stage to further enhance the cleaning process by breaking up contaminants and ensuring more thorough cleaning.
6. Vapor Dwell:
- After the immersion phase, the parts are raised into the vapor zone, where the solvent vapor condenses on the parts, further cleaning them. The condensed solvent then drains back into the process tank.
7. Freeboard Zone:
- The parts are next lifted into the freeboard zone which is fitted with highly efficient Refrigerated Secondary Cooling Plates which are positioned above the cooling coils. In this area, the cooler temperature causes any remaining solvent on the parts or basket to vaporize, which then condenses on the cold surfaces, leaving the parts dry and clean.
- This is the final step before the cleaning cycle ends and the parts are ready for removal.
- If the parts have been immersed in the Boil Tank then a final rinse in the Process Tank, using the same procedure, is performed.
8. Cycle Completion & Part Removal:
- After the parts dwell in the freeboard zone for drying, the system triggers an end-of-cycle alert with both a visual and audible warning.
- The operator presses the door open button, which causes the lid to open and the carrier to rise, bringing the cleaned parts back to the load position where they can be removed.
9. Automatic Operation:
- If the operator does not interact with the system within a preset time, the machine will automatically lower the carrier back to the freeboard zone, and the lid will automatically seal to ensure the process continues until manually interrupted.
Safety Features
The safety features described below for the Layton Low Flashpoint (Flammable) Solvent and Vapor Degreasing system provide a robust system designed to ensure the safe operation of the dryer, especially in environments where flammable vapors, such as those from Isopropyl Alcohol (IPA), Acetone and Cycklohexane, are present.
Here's a breakdown of the safety mechanisms and their functions:
1. Flammable Vapor Detection
- Vapor Detection System: This system is designed to detect the presence of flammable vapors (such as IPA (Iso Propyl Alcohol) vapors) in the air. Detector heads are strategically placed throughout the machine to monitor the environment for any buildup of vapor.
- Lower Explosive Limit (LEL) Monitoring: The system is calibrated to detect when the vapor concentration reaches 20% of the Lower Explosive Limit (LEL). The LEL represents the minimum concentration of vapor in the air required for it to ignite. If the vapor concentration reaches 20% LEL, it is a sign of an unsafe condition.
- Automated Shutdown: If the concentration of flammable vapor reaches the 20% LEL threshold, the control system will automatically disconnect the power by switching off the mains contactor, cutting the electrical supply to the dryer to eliminate any risk of ignition.
- Battery Backup: The vapor detection system is backed by a battery, allowing it to function even if the main power supply is cut off, though this backup is time-limited.
2. Fire Detection and Suppression System
- Flame Detection: The system includes specialized flame detectors designed to detect the presence of flames within the dryer. These sensors are sensitive to even small ignition sources that may occur in the presence of flammable vapors.
- CO2 Fire Suppression: If a flame is detected, the system activates the CO2 fire suppression system. CO2 is released into the main process tank and the air space between the tank and the frame, effectively suppressing any potential fire by displacing oxygen and smothering the flames.
- Control System Integration: The fire detection and suppression system is integrated with the control system and PLC (Programmable Logic Controller), ensuring that the suppression system operates automatically when needed. The system also disconnects the electrical supply to the dryer upon flame detection, preventing any further electrical hazards.
- Safety Circuit Protection: All components of the fire detection system, including detectors, switches, and sensors, are designed to be resistant to faults such as open or short circuits, ensuring reliable operation.
- Battery Backup: Like the vapor detection system, the fire suppression system is powered by a battery, which ensures that the system remains functional even if the main power is lost. However, the backup power is limited and cannot be used indefinitely.
3. Intrinsic Safety Circuits
- Intrinsically Safe Design: The dryer’s control and operating systems are designed with intrinsic safety in mind. This means that the electrical and control systems are built to prevent any possibility of creating a spark or other ignition source that could ignite flammable vapors.
- Approved Barriers: Signaling devices, such as sensors or switches, are routed through approved barriers that serve as interfaces between hazardous and safe areas. These barriers are specifically designed to prevent electrical sparks from reaching the hazardous areas where flammable vapors could accumulate.
- Air-Operated Systems: The valves, cylinders, and motors used in the dryer are either air-operated or ATEX approved, meaning they comply with specific safety standards for equipment used in explosive atmospheres (as per the ATEX directive).
Summary of Key Safety Features:
- Flammable Vapor Detection: Protects the system by automatically shutting it down if the vapor concentration reaches 20% of the LEL.
- Fire Detection and Suppression: Detects flames and discharges CO2 to suppress fires, while removing power from the system to prevent electrical hazards.
- Intrinsic Safety Circuits: Ensures that all control and operating systems are safe for use in potentially hazardous environments by using intrinsically safe designs, air- operated components, and approved barriers.
These safety features work together to minimize the risks associated with flammable solvents, ensuring that the system operates in a controlled, safe manner.
Key Points of Operation:
- Gentle & Efficient Cleaning: The system operates without high-pressure sprays or extreme heat, making it ideal for sensitive parts.
- Closed-Loop Solvent Cycle: The solvent is continuously distilled and reused in a closed-loop system, reducing waste and ensuring consistency.
- Ultrasonic Agitation (if fitted): This helps enhance cleaning efficiency by using high-frequency sound waves to agitate the solvent, breaking up stubborn contaminants.
- Particulate Filtration: This helps enhance cleaning efficiency by ensuring that non- soluble contaminants are removed from the solvent.
- Controlled Environment: The sealed lid, vapor zone, and freeboard zone work together to maintain a controlled environment, ensuring effective cleaning and minimal solvent loss.
Advantages of the System:
- Consistent Quality: The closed-loop distillation and vapor process provide uniform cleaning results across multiple cycles.
- Environmental Benefits: By reusing the solvent and minimizing waste, the system is more environmentally friendly than other cleaning methods.
- Operator-Friendly: The automated cycle with minimal operator intervention ensures ease of use and consistent operation.
- Gentle on Parts: The use of vapor and immersion instead of harsh mechanical or chemical cleaning methods means that the parts are not subject to excessive wear or damage.
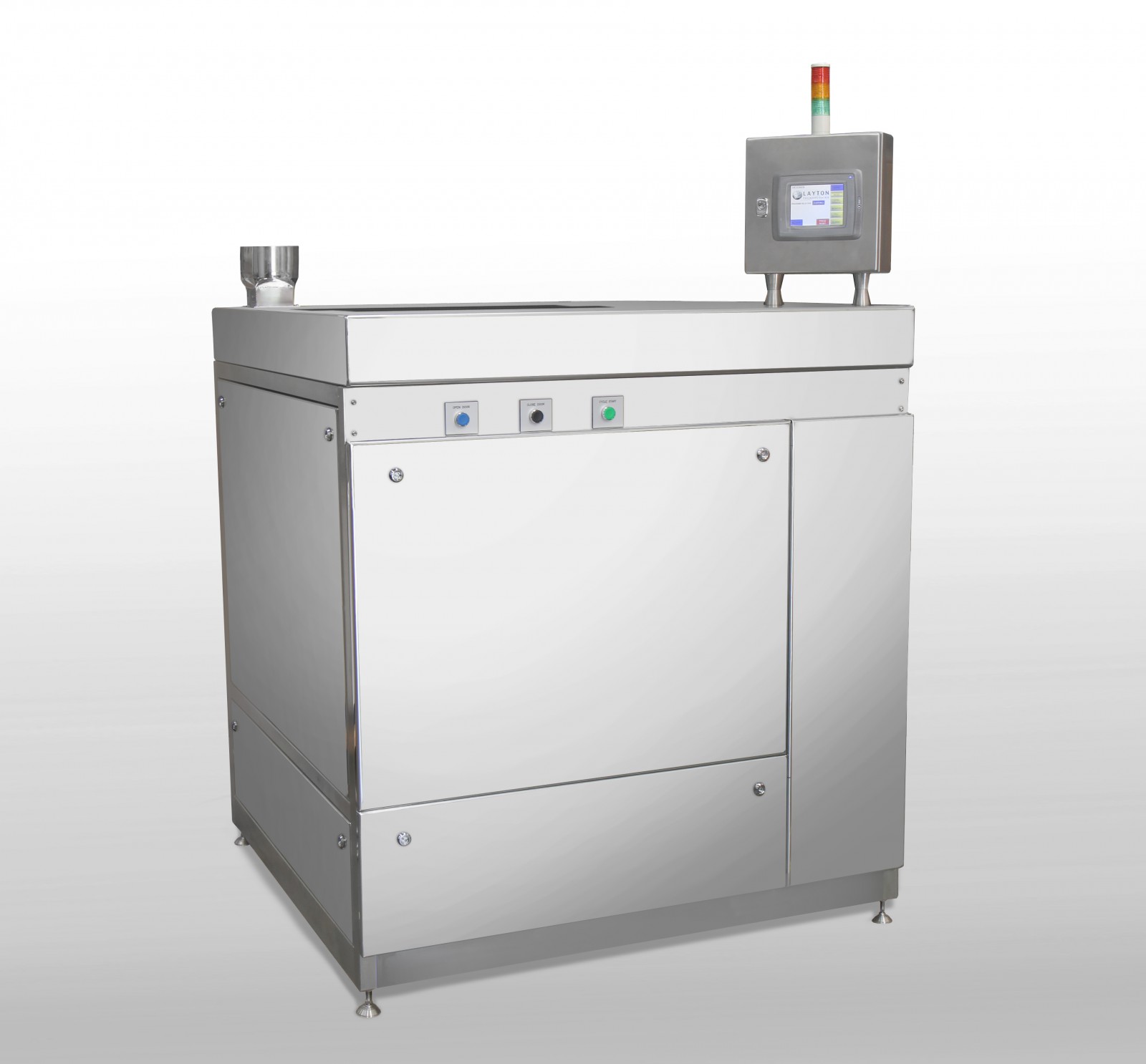
This system provides a highly effective and controlled method for degreasing and cleaning parts, making it ideal for industries where precision and cleanliness are critical, such as electronics, aerospace, and medical device manufacturing.