Multi-Stage Aqueous Ultrasonic Cleaning Equipment
Multi-stage ultrasonic aqueous cleaning equipment refers to a cleaning system that uses ultrasonic waves to remove contaminants from objects by immersing them in water or aqueous solutions.
This type of cleaning is typically employed in industries that require highly effective, precise, and efficient cleaning processes, such as electronics, medical devices, automotive, aerospace, and optics.
The multi-stage process involves multiple cleaning steps that work together to achieve optimal cleaning. Each stage targets a specific part of the cleaning process to ensure thorough removal of contaminants such as oils, dirt, residues, and other particulate matter.
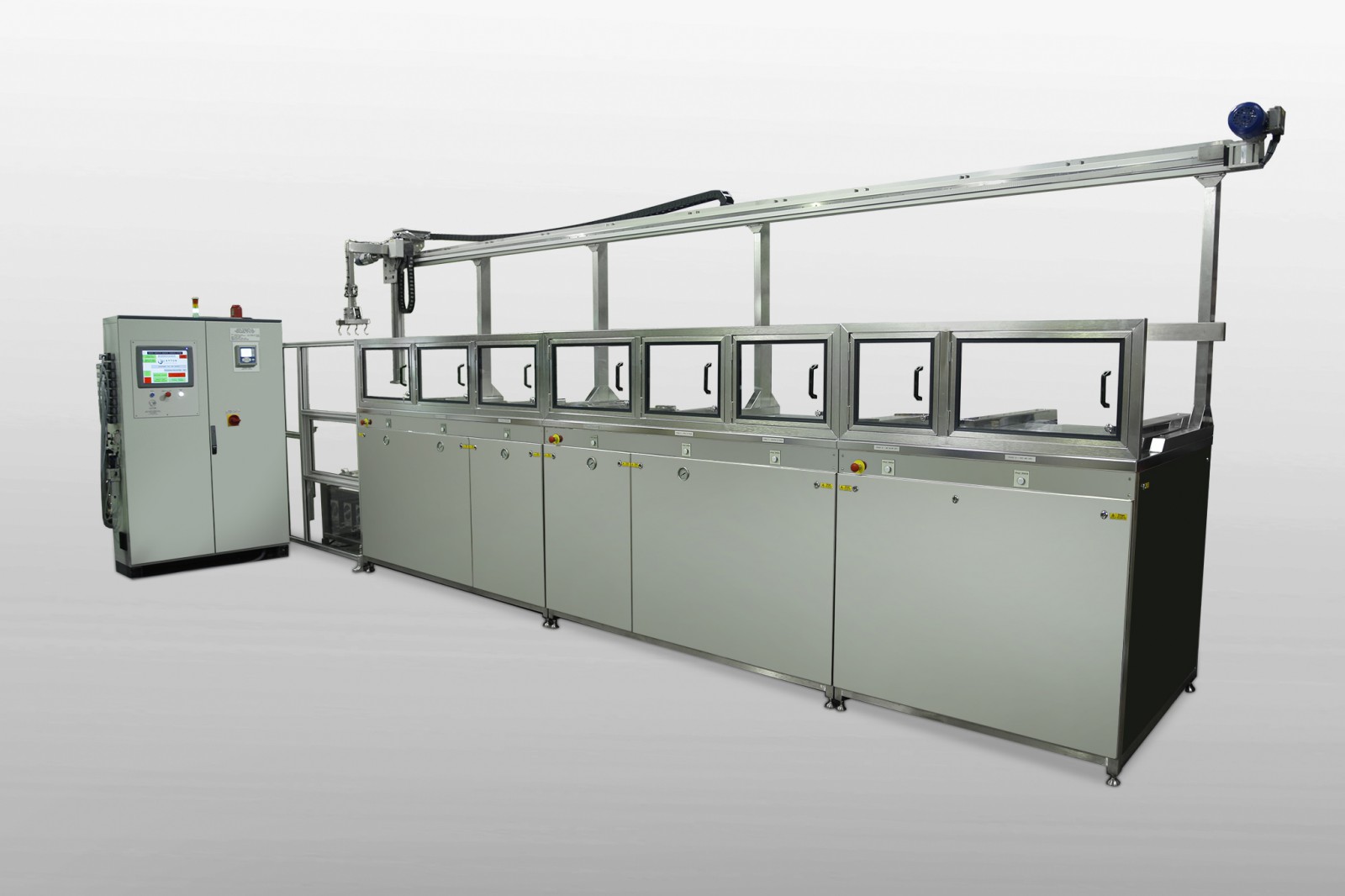
Multi-stage ultrasonic cleaning and passivation system.
Here’s a breakdown of the features, typical stages and key features of our Multi-Stage Ultrasonic Aqueous Cleaning Equipment:
1. Ultrasonic Cavitation:
- The system uses high-frequency sound waves (usually between 20 kHz to 100 kHz) to create microscopic bubbles in a cleaning solution. These bubbles implode on contact with surfaces, dislodging contaminants.
- The cavitation process helps break down stubborn dirt and oil residues without physical brushing, making it suitable for delicate or complex parts.
2. Multiple Cleaning Stages:
- The equipment typically includes several stages, each serving a distinct function in the cleaning process:
- Pre-wash Stage: Often a rinse stage to remove loose particles and contaminants.
- Ultrasonic Cleaning Stage: The core cleaning step where ultrasonic waves are applied to clean the object thoroughly.
- Rinse Stage: To wash away any remaining cleaning solution or particles from the ultrasonic process.
- Drying Stage: Some systems include an additional drying step using hot air or heat to remove residual moisture.
3. Aqueous Solutions:
- The cleaning process uses water-based solutions, often enhanced with detergents or special cleaners designed to target specific contaminants (e.g., oils, greases, flux, dust). The use of aqueous solutions makes it more environmentally friendly compared to solvent-based cleaners.
4. Temperature Control:
- Many multi-stage systems have temperature control features. The ultrasonic cleaning process is typically more effective at higher temperatures, as it helps to accelerate the cavitation process and enhance the overall cleaning efficiency.
5. Filtration System:
- Filtration systems are often incorporated to remove particulate matter from the solution, ensuring that the cleaning process remains effective and preventing re-contamination of the parts.
6. Customization:
- Modern ultrasonic cleaning systems can be customized to handle different parts and cleaning requirements, whether that’s for delicate electronics or robust automotive components.
Typical Multi-Stage Cleaning Process:
1. Stage 1: Pre-Wash
- The part is initially washed with water or a mildly abrasive detergent to
remove larger debris or loose contaminants.
- The part is initially washed with water or a mildly abrasive detergent to
2. Stage 2: Ultrasonic Cleaning
- The part is placed in a tank filled with an aqueous solution. High-frequency
sound waves are applied, creating cavitation bubbles that gently clean the
object’s surface by removing oils, grease, and small particles.
- The part is placed in a tank filled with an aqueous solution. High-frequency
3. Stage 3: Rinsing
- The part is rinsed with clean water or a rinse solution to remove any residual
cleaning solution and contaminants loosened during the ultrasonic cleaning
stage.
- The part is rinsed with clean water or a rinse solution to remove any residual
4. Stage 4: Drying (optional)
- After rinsing, the part may be dried using warm air, heated platforms, or
vacuum systems, depending on the requirements for the application.
- After rinsing, the part may be dried using warm air, heated platforms, or
Applications:
- Electronics Manufacturing: Cleaning components like PCBs, semiconductors, and microchips.
- Medical Devices: Removing biological and chemical contaminants from surgical instruments and implants.
- Automotive and Aerospace: Cleaning engine parts, precision components, and assemblies.
- Optical Devices: Removing contaminants from lenses and mirrors without causing damage.
- Jewelry and Watches: Cleaning delicate and intricate pieces without damage.
Advantages:
- Gentle but Effective: The ultrasonic waves can clean delicate parts without causing physical damage.
- Thorough Cleaning: Capable of cleaning parts with complex geometries, hidden crevices, and hard-to-reach areas.
- Environmentally Friendly: Using water-based solutions reduces the reliance on harmful chemicals and solvents.
- Consistency: Provides consistent, repeatable results, crucial for high-precision applications.
Considerations:
- Cost: Multi-stage ultrasonic cleaning systems can be expensive due to the advanced technology involved.
- Maintenance: Regular maintenance of the tanks, transducers, and filtration systems is necessary for optimal performance.
- Size of Parts: The equipment should be sized correctly for the parts being cleaned to ensure efficiency.
In conclusion, multi-stage ultrasonic aqueous cleaning systems are an advanced and highly efficient method for cleaning parts and components in various industries. They offer precise, consistent cleaning without damaging delicate items, making them a preferred choice for sensitive and intricate cleaning tasks.
Infinitely variable equipment for precision component cleaning, degreasing, passivation and drying applications.