IPA Vapor Dryer
Single stage IPA solvent vapor component drying machine for critical applications
Link to the Vapor Dryer whitepaper.
An IPA (Isopropyl Alcohol) vapour dryer is a device used to dry components or surfaces by utilizing IPA vapor as the drying medium. This process is often used in industries where precision cleaning and drying are necessary, such as in electronics, semiconductor manufacturing, or medical device production.
An IPA (Iso-propyl alcohol) method uses a water solubilization mechanism for complete removal of water measured down to molecular level. The technology uses IPA to absorb surface water. With an extremely low surface tension rating, the IPA permeates surface cracks, line geometries and deep trenches.
The system works with a single-tank design to provide efficient cleaning and drying through a thermally controlled vapor process. The choice of configuration is, generally, dependent upon the level of contamination to be removed from the parts.
Here's a breakdown of how the system operates:
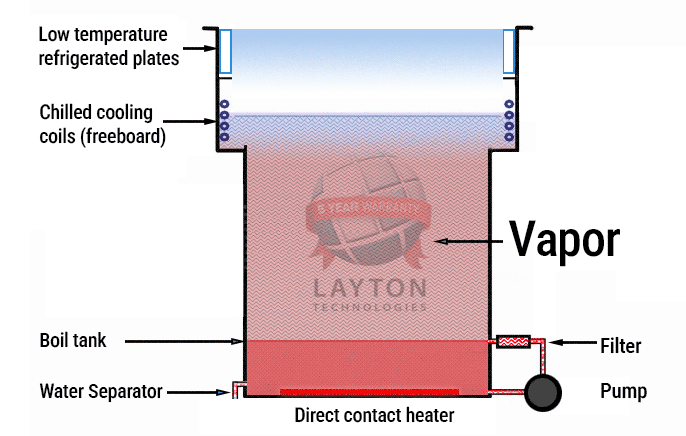
Vapor Dryer diagram image copyright Layton Technologies
System Overview:
- Single Tank System: The system uses a single process tank designed to minimize the first fill solvent requirement by reusing the solvent through a distillation cycle. The solvent is boiled here to create vapor. This vapor rises and forms a blanket around the mid-point of the cooling coils, promoting condensation.
- Vapor Zone: The area where the solvent vapor condenses on the cooling coils, transferring the solvent back to the base of the process tank. This ensures continuous distillation of the solvent.
- Carrier and Platform: Parts to be cleaned or dried are placed on a suitable carrier. The carrier is then positioned on the work platform located directly beneath a sealed sliding lid.
- Operator Interaction: The operator starts the cycle by pressing a button, which lowers the platform to the vapor zone. The lid is sealed, ensuring the process remains enclosed.
Step-by-Step Process
- Loading Parts: The operator loads parts onto the carrier and places it on the work platform beneath the sealed lid.
- Split lid which operates in two opposite directions using pneumatic cylinders. The closure mechanism allows for the arm to move up and down while the lids are closed.
- Vapor Dwell: Once the platform is lowered to the vapor zone, the parts are exposed to the solvent vapor. The vapor condenses on the parts, creating a mixture of solvent and water, which strips away any moisture.
- Collection and Disposal: The solvent/water mixture falls into a specially designed tray at the bottom of the process tank, preventing it from mixing with the boiling solvent. This mixture is diverted to a small buffer tank, which is periodically drained to a facility effluent drain.
- Freeboard Zone: After the solvent dwell, the platform is raised into the freeboard zone, where the cool atmosphere causes any remaining solvent on the parts to vaporize. This vapor condenses on the cold plates above the parts.
- Cycle Completion: After the freeboard dwell, the process is complete. An audible and visual alarm signals the end of the cycle, prompting the operator to open the door, remove the parts, and reload if necessary.
Operational Controls
- Sealed Sliding Lid: Ensures the process is enclosed and solvent vapor is contained within the system during the cycle.
- Cycle Start/End: The operator initiates the cycle via the start button, and the process ends with an alarm. The lid automatically opens after the cycle, and the platform returns to the load position.
- Automatic Lid Closure: The sliding lid closes automatically after a set time of inactivity, ensuring no vapor escapes when the system is idle.
Maintenance and Environmental Considerations
- Effluent Handling: The water-solvent mixture collected in the buffer tank is periodically drained out of the system to prevent contamination of the boiling solvent and ensure the proper environmental disposal of waste.
- Continuous Solvent Reuse: By condensing the solvent vapor back into liquid form, the system allows for the reuse of solvent, making it more efficient and reducing solvent waste.
Key Benefits
- Efficiency: The use of vapor condensation allows for the continuous distillation of the solvent, reducing the amount of fresh solvent required.
- Reduced Environmental Impact: The collection and periodic disposal of the water- solvent mixture help minimize environmental contamination, with waste sent to a dedicated effluent drain.
- Operator Safety: The sealed environment and automatic features (e.g., automatic lid closure, audible alarms) improve operator safety and system reliability.
Safety Features
The safety features described below for the IPA vapor dryer provide a robust system designed to ensure the safe operation of the dryer, especially in environments where flammable vapors, such as those from Isopropyl Alcohol (IPA), are present.
Here's a breakdown of the safety mechanisms and their functions:
1. Flammable Vapor Detection
- Vapor Detection System: This system is designed to detect the presence of flammable vapors (such as IPA (Iso Propyl Alcohol) vapors) in the air. Detector heads are strategically placed throughout the machine to monitor the environment for any buildup of vapor.
- Lower Explosive Limit (LEL) Monitoring: The system is calibrated to detect when the vapor concentration reaches 20% of the Lower Explosive Limit (LEL). The LEL represents the minimum concentration of vapor in the air required for it to ignite. If the vapor concentration reaches 20% LEL, it is a sign of an unsafe condition.
- Automated Shutdown: If the concentration of flammable vapor reaches the 20% LEL threshold, the control system will automatically disconnect the power by switching off the mains contactor, cutting the electrical supply to the dryer to eliminate any risk of ignition.
- Battery Backup: The vapor detection system is backed by a battery, allowing it to function even if the main power supply is cut off, though this backup is time- imited.
2. Fire Detection and Suppression System
- Flame Detection: The system includes specialized flame detectors designed to detect the presence of flames within the dryer. These sensors are sensitive to even small ignition sources that may occur in the presence of flammable vapors.
- CO2 Fire Suppression: If a flame is detected, the system activates the CO2 fire suppression system. CO2 is released into the main process tank and the air space between the tank and the frame, effectively suppressing any potential fire by displacing oxygen and smothering the flames.
- Control System Integration: The fire detection and suppression system is integrated with the control system and PLC (Programmable Logic Controller), ensuring that the suppression system operates automatically when needed. The system also disconnects the electrical supply to the dryer upon flame detection, preventing any further electrical hazards.
- Safety Circuit Protection: All components of the fire detection system, including detectors, switches, and sensors, are designed to be resistant to faults such as open or short circuits, ensuring reliable operation.
- Battery Backup: Like the vapor detection system, the fire suppression system is powered by a battery, which ensures that the system remains functional even if the main power is lost. However, the backup power is limited and cannot be used indefinitely.
3. Intrinsic Safety Circuits
- Intrinsically Safe Design: The dryer’s control and operating systems are designed with intrinsic safety in mind. This means that the electrical and control systems are built to prevent any possibility of creating a spark or other ignition source that could ignite flammable vapors.
- Approved Barriers: Signaling devices, such as sensors or switches, are routed through approved barriers that serve as interfaces between hazardous and safe areas. These barriers are specifically designed to prevent electrical sparks from reaching the hazardous areas where flammable vapors could accumulate.
- Air-Operated Systems: The valves, cylinders, and motors used in the dryer are either air-operated or ATEX approved, meaning they comply with specific safety standards for equipment used in explosive atmospheres (as per the ATEX directive).
Summary of Key Safety Features:
- Flammable Vapor Detection: Protects the system by automatically shutting it down if the vapor concentration reaches 20% of the LEL.
- Fire Detection and Suppression: Detects flames and discharges CO2 to suppress fires, while removing power from the system to prevent electrical hazards.
- Intrinsic Safety Circuits: Ensures that all control and operating systems are safe for use in potentially hazardous environments by using intrinsically safe designs, air- operated components, and approved barriers.
These safety features work together to minimize the risks associated with flammable IPA vapors, ensuring that the IPA vapor drying system operates in a controlled, safe manner.
Case Study 1: Vapor degreaser machine using an azeotropic blend of Cyclohexane and IPA for cleaning of electronic components.
This Vapor degreaser machine is designed to safely use an azeotropic blend of Cyclohexane and IPA for cleaning of electronic components. This azeotrope has been shown to be effective in removing a wide variety of contaminants since alcohol’s polar molecular chemistry results in repulsion forces between particles and the surface. These forces tend to shield the effect of van der Waals forces and dissipate electrostatic forces to the extent that alcohol is approximately twice as effective for removal of micron-sized particles than water.
Cyclohexane, a solvent with physical properties similar to alcohol, is effective for removing organic films (oil and grease) when used in similar equipment. The drying of the components is carried out in the vapour phase and freeboard area below the sealed sliding lid. The components can be immersed and/or sprayed. The spray pressure can be controlled for particularly fragile components. There is a minimal footprint together with ease of maintenance.